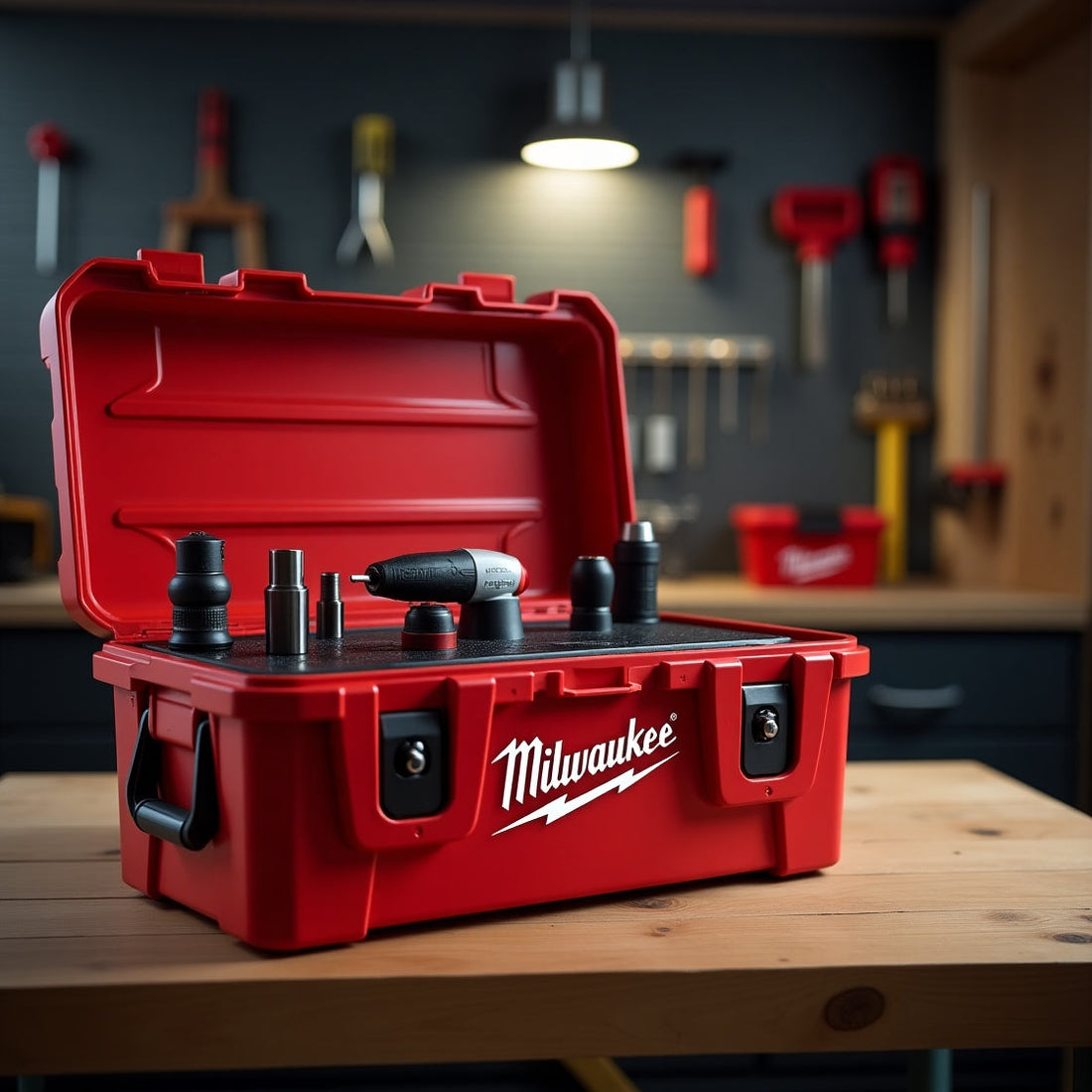
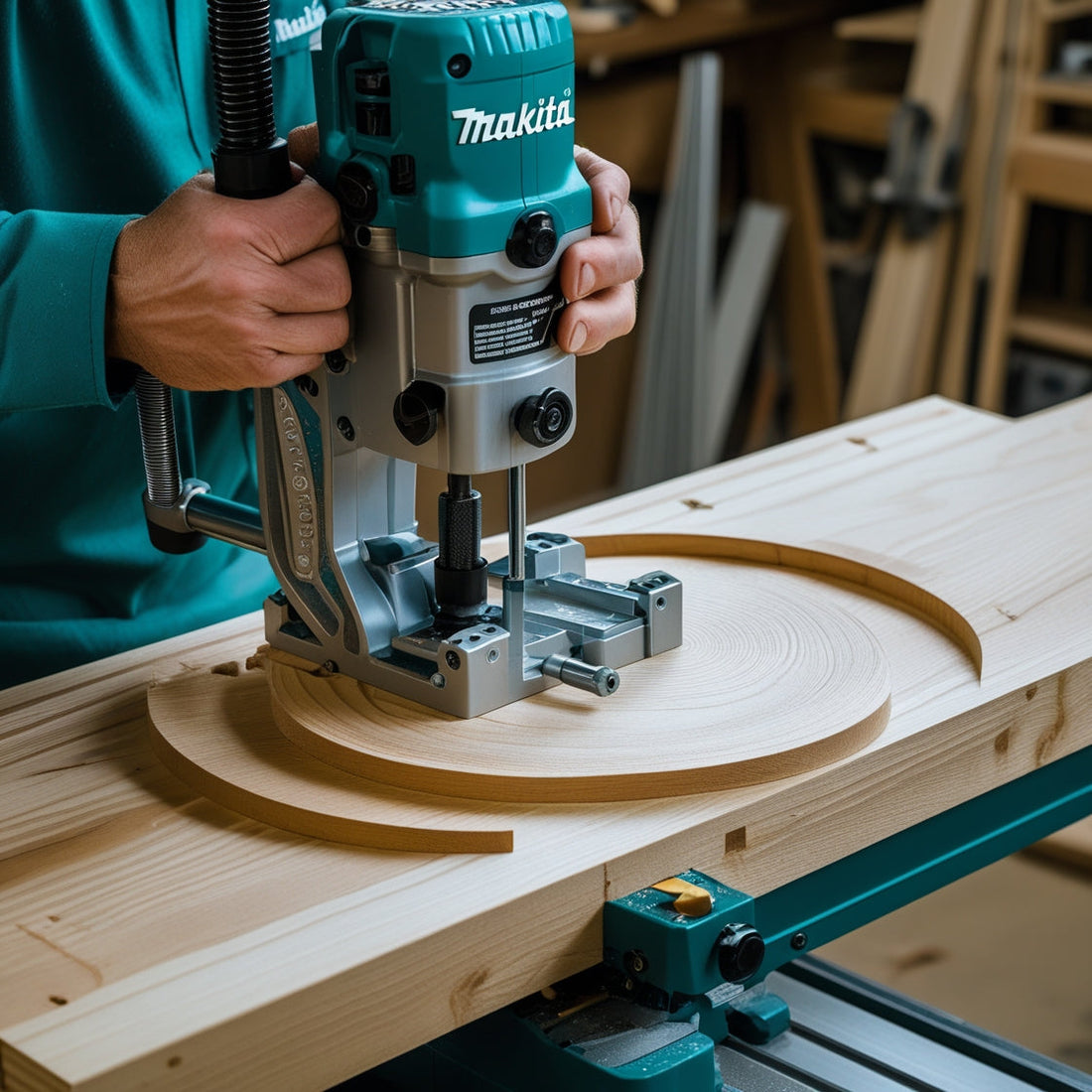
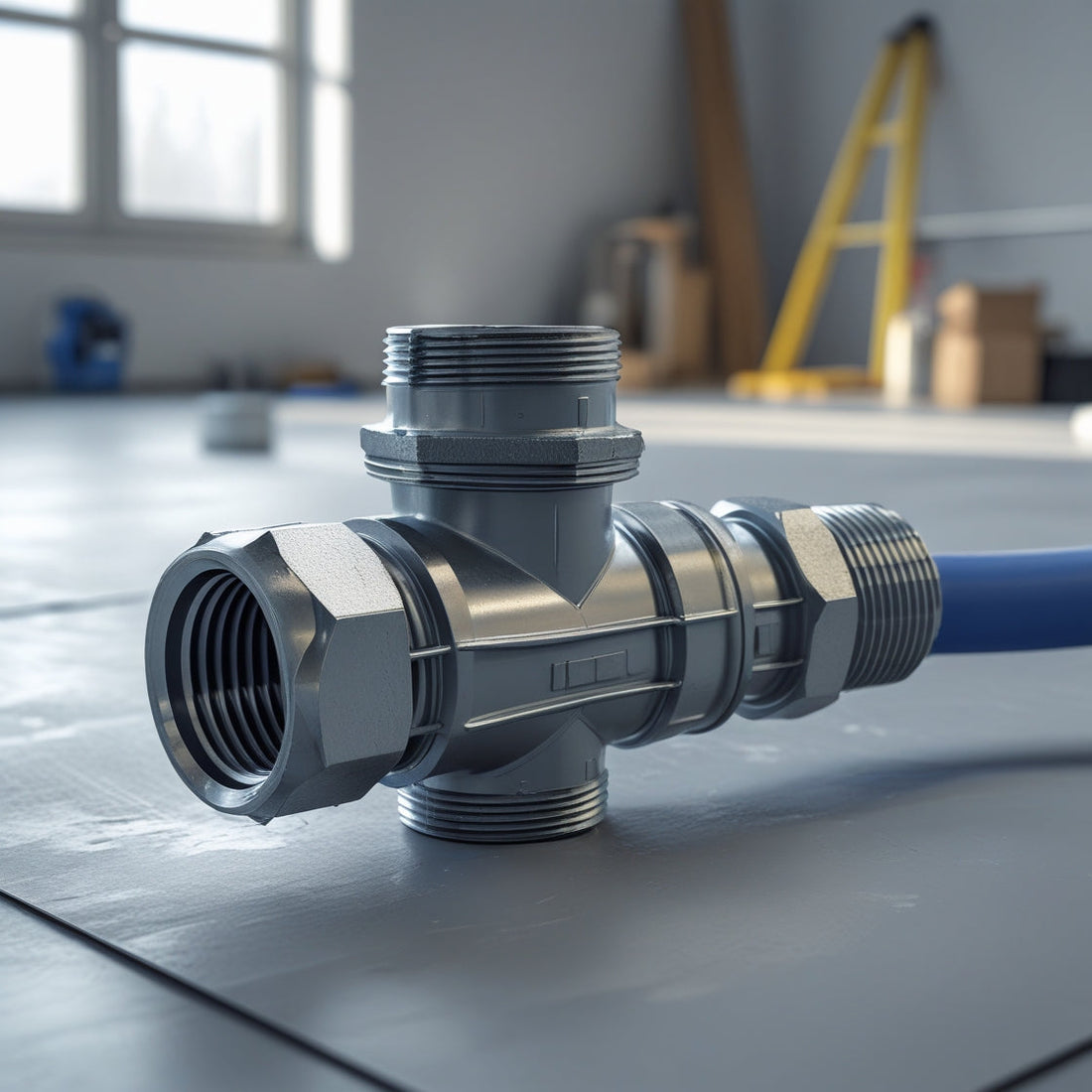
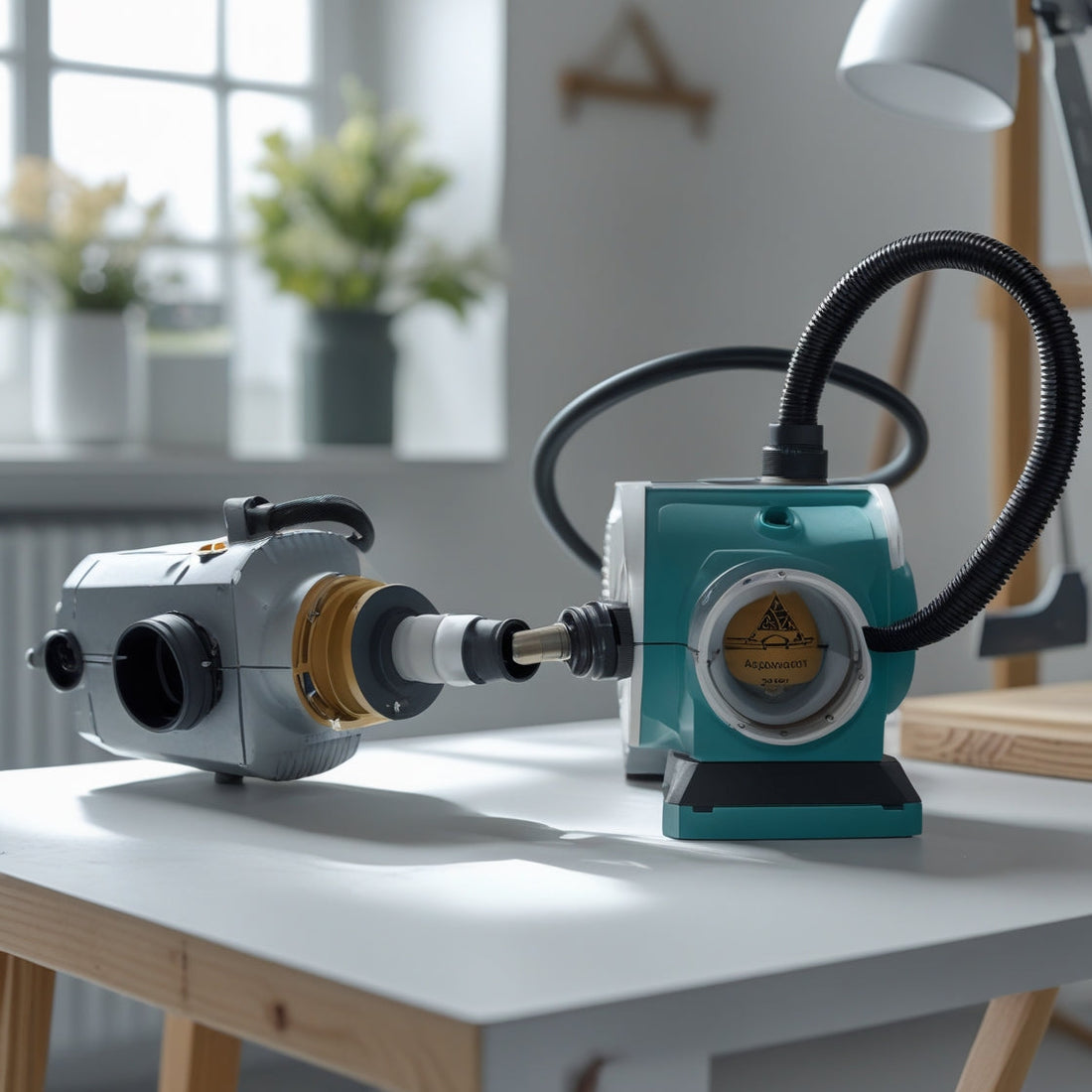
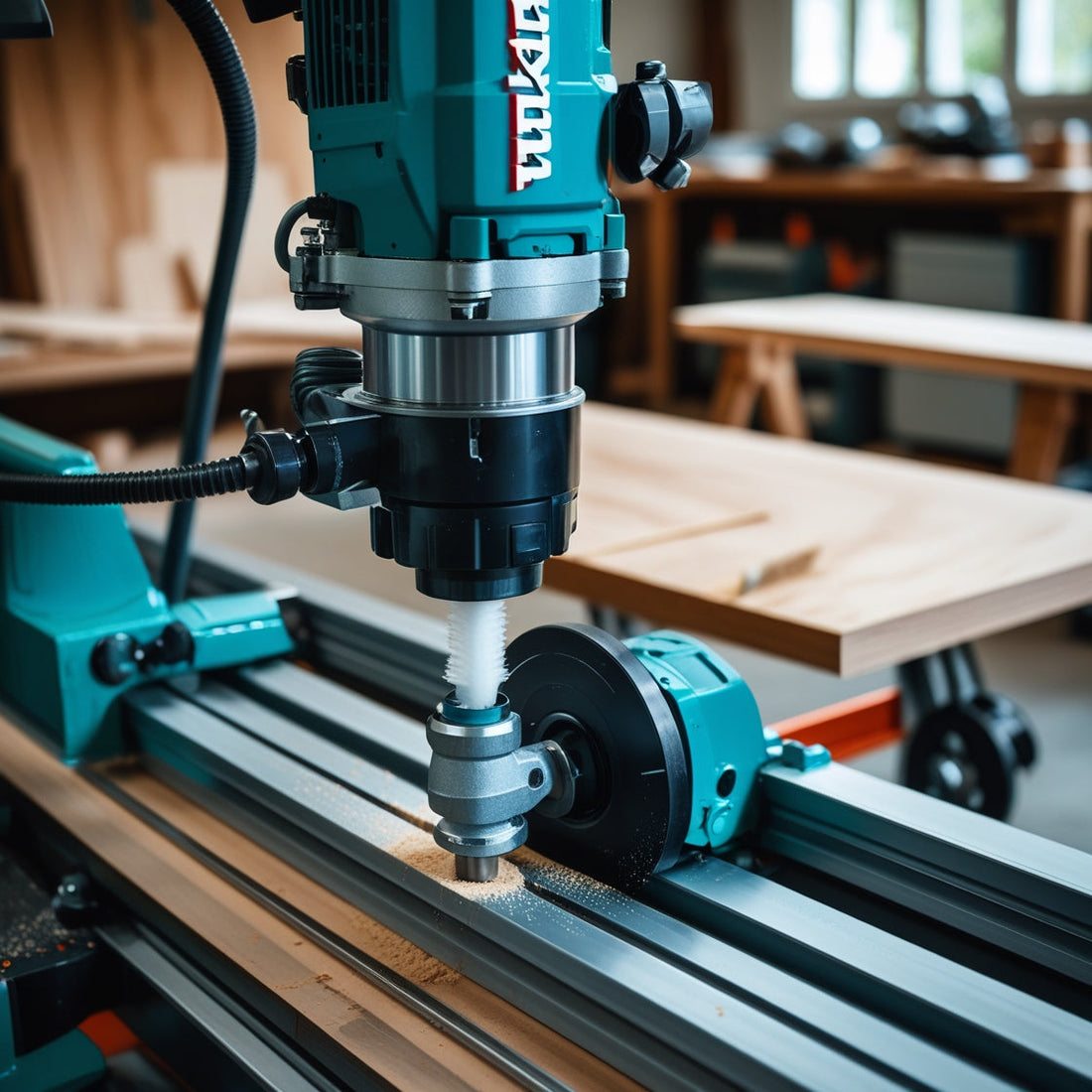


Applications industrielles : optimiser la production et l'efficacité - Un guide complet
Applications industrielles : un aperçu complet
Les applications industrielles représentent un domaine en constante évolution, crucial pour l'optimisation des processus de production et l'amélioration de la compétitivité des entreprises. Elles englobent une multitude de technologies et de solutions visant à améliorer l'efficacité, la productivité, la sécurité et la rentabilité des opérations industrielles, quel que soit le secteur d'activité : manufacturier, énergétique, agroalimentaire, logistique, etc. Du contrôle précis des paramètres de production à la maintenance prédictive en passant par la robotique collaborative, l'analyse de données sophistiquée, la réalité augmentée et la chaîne logistique intelligente, ces applications transforment profondément les méthodes de travail et les modèles économiques. L'objectif principal est de créer une production plus intelligente, plus flexible et plus résiliente, capable de s'adapter aux exigences changeantes du marché et de la concurrence.
Cet article explore en détail les différentes applications industrielles, leurs avantages, leurs défis et comment elles contribuent à une optimisation globale des opérations, en soulignant les aspects économiques, environnementaux et sociaux. Nous analyserons également les différents modèles d'implémentation et les stratégies pour assurer une transition réussie vers l'industrie 4.0.
Les principaux domaines d'applications industrielles : une analyse détaillée
1. Automatisation industrielle et Robotique collaborative
L'automatisation des processus, y compris l'intégration de robots collaboratifs (cobots), permet d'augmenter la productivité, de réduire les coûts de main-d'œuvre, d'améliorer la qualité et la précision des produits, et de gérer les tâches répétitives, pénibles ou dangereuses pour les humains. L'automatisation peut concerner des opérations de soudage, de peinture, d'assemblage, de manutention, de palettisation, d'inspection qualité, etc. Les robots industriels sont de plus en plus sophistiqués, intégrant des capteurs avancés, des systèmes de vision artificielle et des systèmes d'intelligence artificielle pour une plus grande autonomie, adaptabilité et collaboration avec les opérateurs humains. L'intégration de l'intelligence artificielle permet également une meilleure optimisation des trajectoires robotisées, des ajustements en temps réel et une meilleure gestion des imprévus.
2. Maintenance prédictive et Internet des Objets (IoT)
Grâce à la collecte de données en temps réel provenant de capteurs connectés (Internet des objets - IoT) intégrés aux machines et équipements, la maintenance prédictive permet d'anticiper les pannes d'équipement. L'analyse de ces données, souvent couplée à des algorithmes d'apprentissage automatique (Machine Learning), permet de prévoir les défaillances et de programmer des interventions de maintenance de manière proactive, minimisant ainsi les temps d'arrêt coûteux et les pertes de production. L'IoT joue un rôle crucial en facilitant la connexion et le partage d'informations entre les différents équipements et systèmes, créant une véritable synergie numérique au sein de l'usine.
3. Contrôle des processus et Supervision industrielle
Des systèmes de contrôle-commande avancés, souvent basés sur des systèmes SCADA (Supervisory Control and Data Acquisition), surveillent et régulent les processus de production en temps réel, garantissant la qualité, la cohérence et la conformité des produits finis. Ces systèmes permettent d'optimiser l'utilisation des ressources (énergie, matières premières, eau), de minimiser les déchets, d'améliorer le rendement global et de réduire les coûts de production. La supervision permet une surveillance centralisée des différents paramètres et une intervention rapide en cas d'anomalies ou de déviations par rapport aux standards définis. Les tableaux de bord numériques offrent une vision globale de l'état du processus de production.
4. Gestion de l'énergie et Efficacité énergétique
L'optimisation de la consommation énergétique est un enjeu majeur pour les entreprises industrielles, tant sur le plan économique qu'environnemental. Les applications industrielles permettent de surveiller, d'analyser et de gérer la consommation d'énergie en détail, en identifiant les sources de pertes et en proposant des solutions pour améliorer l'efficacité énergétique. Cela peut inclure l'utilisation de technologies intelligentes pour optimiser les systèmes de chauffage, de climatisation, d'éclairage, les moteurs électriques, etc. L'analyse des données permet d'identifier les périodes de forte consommation et d'adapter la production en conséquence, tout en optimisant l'utilisation des énergies renouvelables.
5. Systèmes de gestion de la qualité et de la conformité
La gestion de la qualité est un aspect crucial dans l'industrie moderne. Des applications spécifiques permettent de mettre en place des systèmes de gestion de la qualité intégrés, conformes aux normes ISO (ISO 9001, ISO 14001, etc.), et de suivre les indicateurs clés de performance (KPI) en temps réel. La traçabilité des produits, le contrôle de la qualité à chaque étape du processus et la gestion des non-conformités sont autant d'aspects améliorés grâce aux outils numériques. Cela permet d'améliorer la satisfaction client et de réduire les coûts liés aux produits défectueux.
6. Sécurité industrielle et Gestion des risques
La sécurité des travailleurs et la prévention des accidents sont des priorités absolues. Les applications industrielles contribuent à créer un environnement de travail plus sûr grâce à des systèmes de surveillance, d'alerte et de protection. Cela peut inclure des capteurs de gaz, des systèmes de détection d'incendie, des dispositifs de protection individuelle connectés, des systèmes de gestion des risques et des simulations de scénarios d'accidents. L'analyse des données permet d'identifier les zones à risque et de mettre en place des mesures de prévention adaptées.
7. Intelligence Artificielle (IA) et Machine Learning (ML)
L'IA et le ML sont de plus en plus utilisés pour analyser des données complexes, optimiser les processus de production, améliorer la prévision de la demande, automatiser des tâches complexes et détecter des anomalies en temps réel. L'apprentissage automatique permet aux systèmes d'apprendre à partir des données et d'améliorer leurs performances au fil du temps, en s'adaptant aux variations des conditions de production. L'IA peut être utilisée pour la maintenance prédictive, le contrôle qualité, l'optimisation de la planification de la production et la prise de décision.
8. Big Data et Analyse prédictive
La collecte et l'analyse de vastes quantités de données (Big Data) permettent d'identifier des tendances, des patterns et des anomalies dans les processus de production. L'analyse prédictive permet de prévoir les événements futurs, tels que les pannes d'équipement, les variations de la demande ou les risques de sécurité, afin de prendre des décisions éclairées et d'optimiser les opérations. L'analyse des données peut également aider à optimiser la chaîne logistique, à réduire les stocks et à améliorer la gestion des ressources.
9. Simulation et jumeaux numériques
La simulation permet de tester et d'optimiser des processus virtuellement avant leur mise en œuvre dans l'environnement réel, réduisant ainsi les risques et les coûts associés. Les jumeaux numériques, des représentations virtuelles des équipements et des processus, permettent de surveiller, d'analyser et de contrôler les opérations à distance, facilitant la maintenance, l'optimisation et la formation des opérateurs. Cela permet de tester différents scénarios et d'identifier les meilleures solutions avant leur implémentation physique.
10. Réalité augmentée (RA) et Réalité virtuelle (RV)
La réalité augmentée et la réalité virtuelle offrent de nouvelles possibilités pour la formation des opérateurs, la maintenance et l'assistance technique à distance. La RA permet de superposer des informations numériques sur le monde réel, facilitant la maintenance et la réparation des équipements. La RV permet de simuler des situations réelles et de former les opérateurs dans un environnement sûr et contrôlé.
11. Chaîne logistique intelligente
La digitalisation de la chaîne logistique permet une meilleure visibilité, une meilleure coordination et une meilleure optimisation des flux de marchandises. Des applications industrielles permettent de suivre les produits en temps réel, d'optimiser les transports, de gérer les stocks et d'améliorer la collaboration entre les différents acteurs de la chaîne logistique.
Avantages et défis des applications industrielles
Avantages :
- Amélioration significative de la productivité et de l'efficacité.
- Réduction des coûts de production et des déchets.
- Amélioration de la qualité des produits et de la conformité.
- Augmentation de la sécurité et de la protection des travailleurs.
- Gain de compétitivité sur le marché.
- Optimisation de la gestion des ressources (énergie, matières premières).
- Amélioration de la prise de décision grâce à l'analyse de données.
- Flexibilité accrue et adaptation aux changements du marché.
- Amélioration de la collaboration entre les différents acteurs de la chaîne de valeur.
Défis :
- Coûts d'investissement initiaux importants.
- Nécessité d'une expertise technique et de compétences spécifiques.
- Intégration complexe des différents systèmes et technologies.
- Sécurité des données et cybersécurité.
- Adaptation au changement et formation du personnel.
- Maintenance et mise à jour des systèmes.
- Gestion du changement organisationnel.
Conclusion
Les applications industrielles sont des éléments clés de la transformation numérique et de l'industrie 4.0. L'adoption de ces technologies offre des avantages considérables en termes d'efficacité, de productivité, de sécurité et de compétitivité. Cependant, la mise en œuvre réussie nécessite une planification rigoureuse, une expertise technique appropriée et une gestion efficace des risques. La collaboration entre les fabricants, les intégrateurs, les consultants et les utilisateurs est essentielle pour maximiser le retour sur investissement et garantir une transition réussie vers une production plus intelligente, plus durable et plus résiliente. Une stratégie bien définie, incluant la formation du personnel et la gestion du changement organisationnel, est primordiale pour la réussite de l'implémentation de ces technologies.
Mots clés :
Applications industrielles, automatisation, robotique, IoT, maintenance prédictive, contrôle des processus, gestion de l'énergie, sécurité industrielle, intelligence artificielle, machine learning, Big Data, analyse prédictive, simulation, jumeaux numériques, réalité augmentée, réalité virtuelle, chaîne logistique intelligente, industrie 4.0, optimisation de la production, efficacité énergétique, transformation numérique, compétitivité industrielle, gestion de la qualité, SCADA, KPI, ISO 9001, ISO 14001.