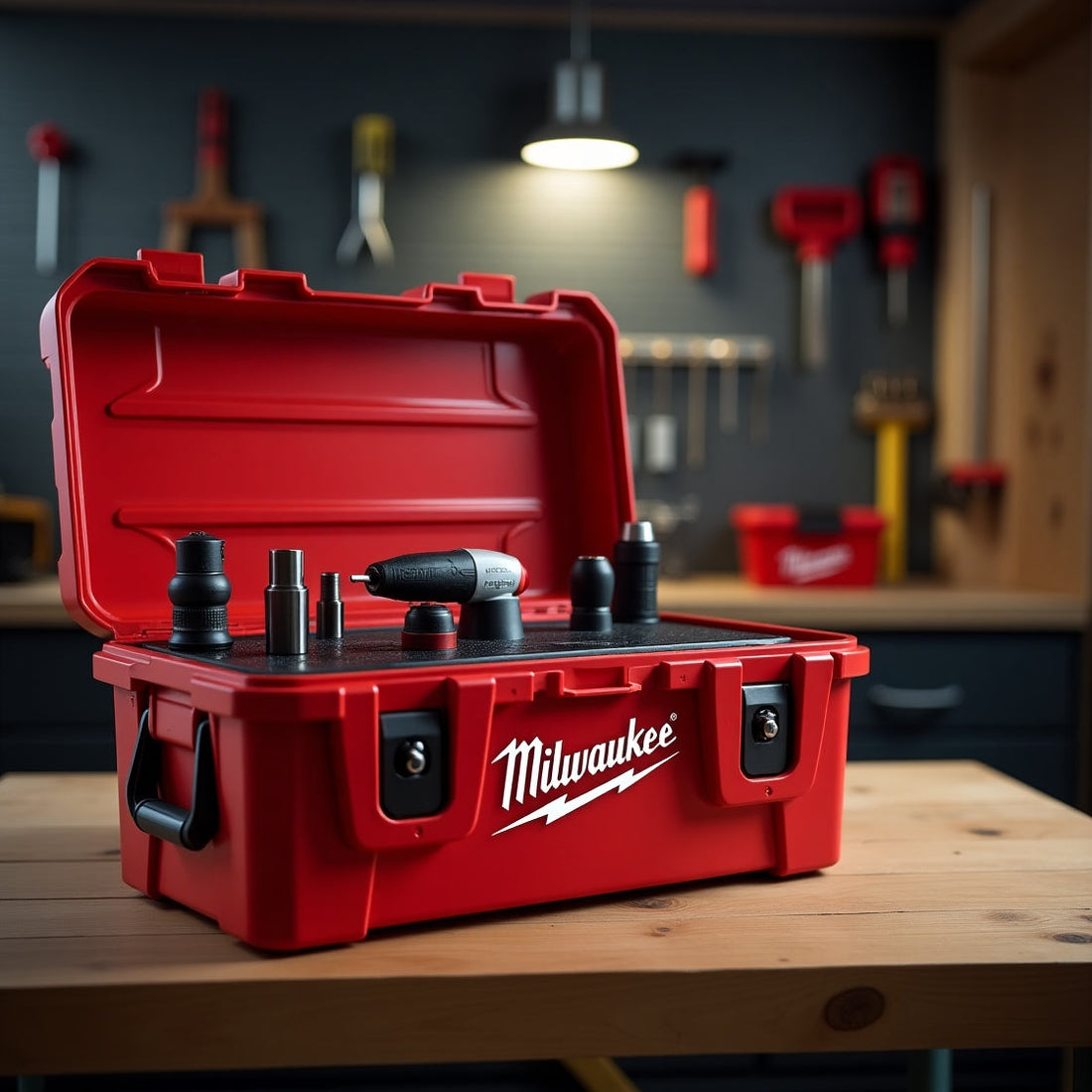
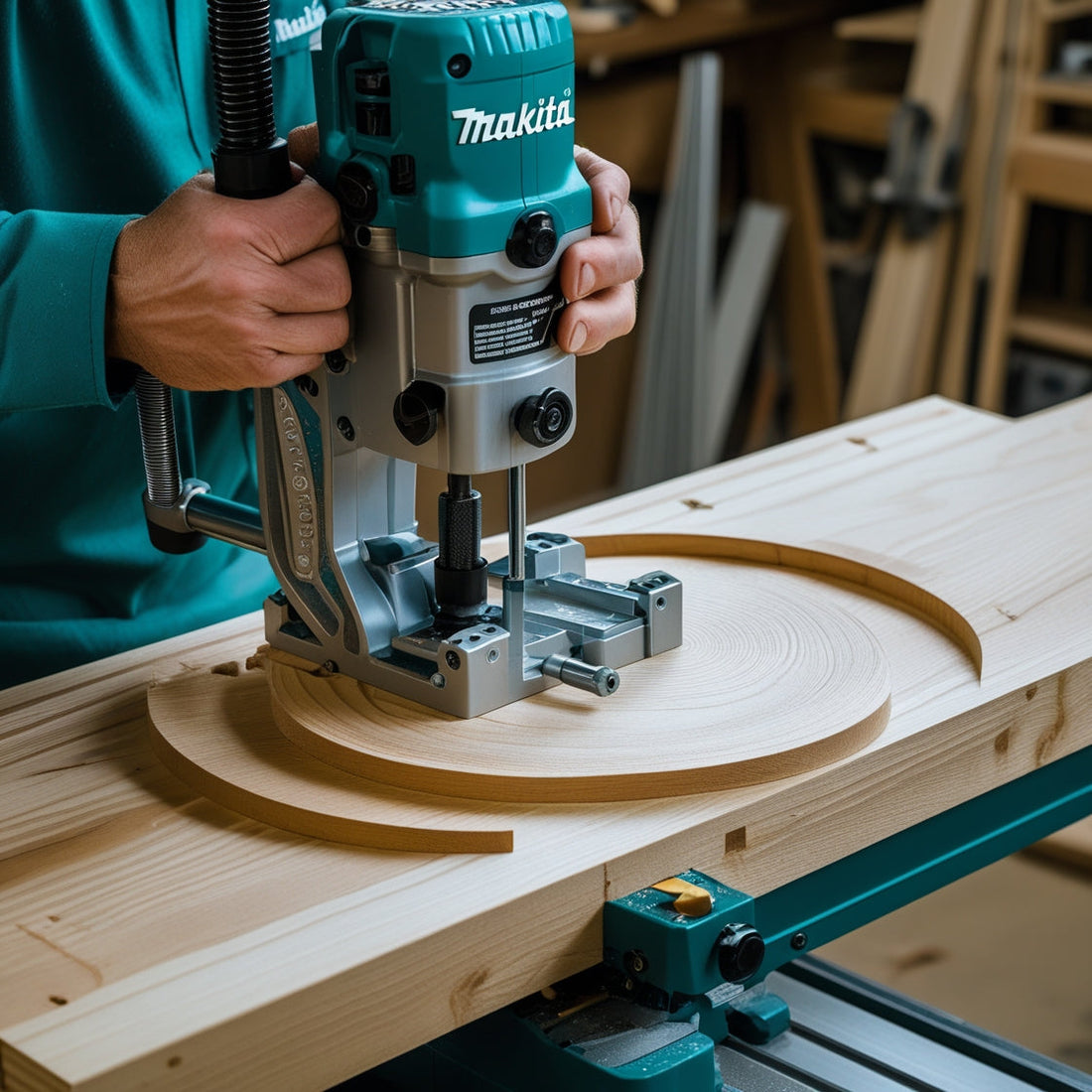
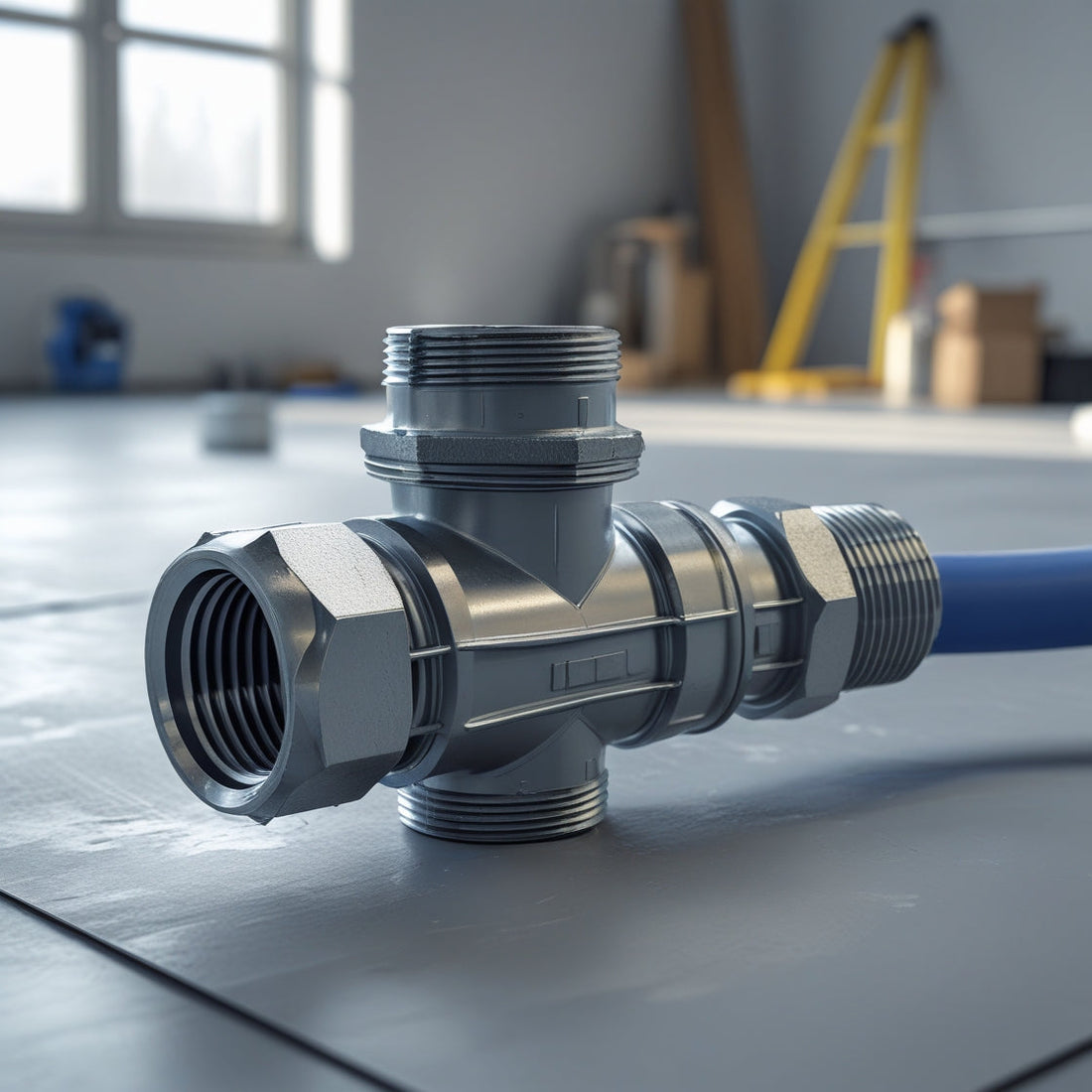
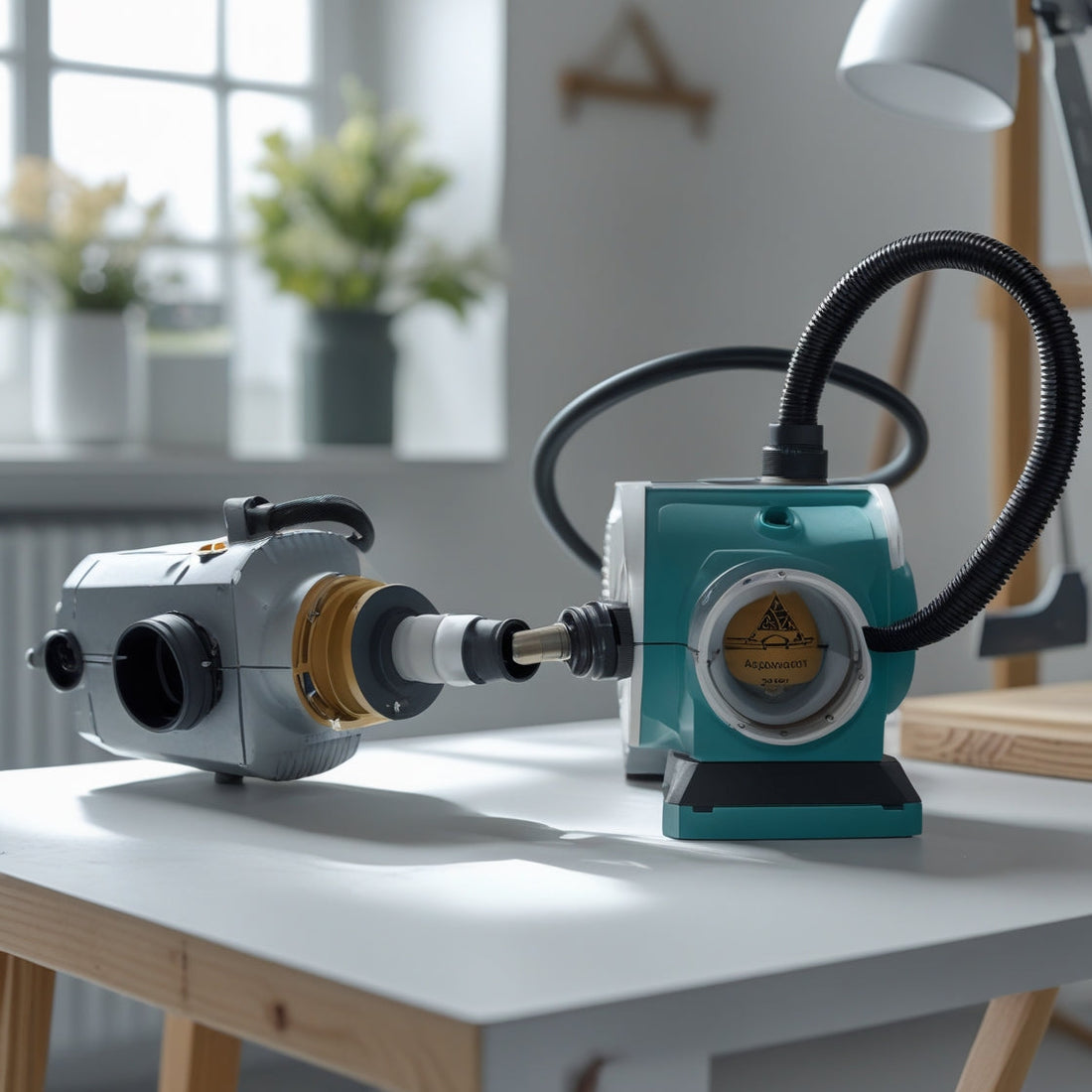
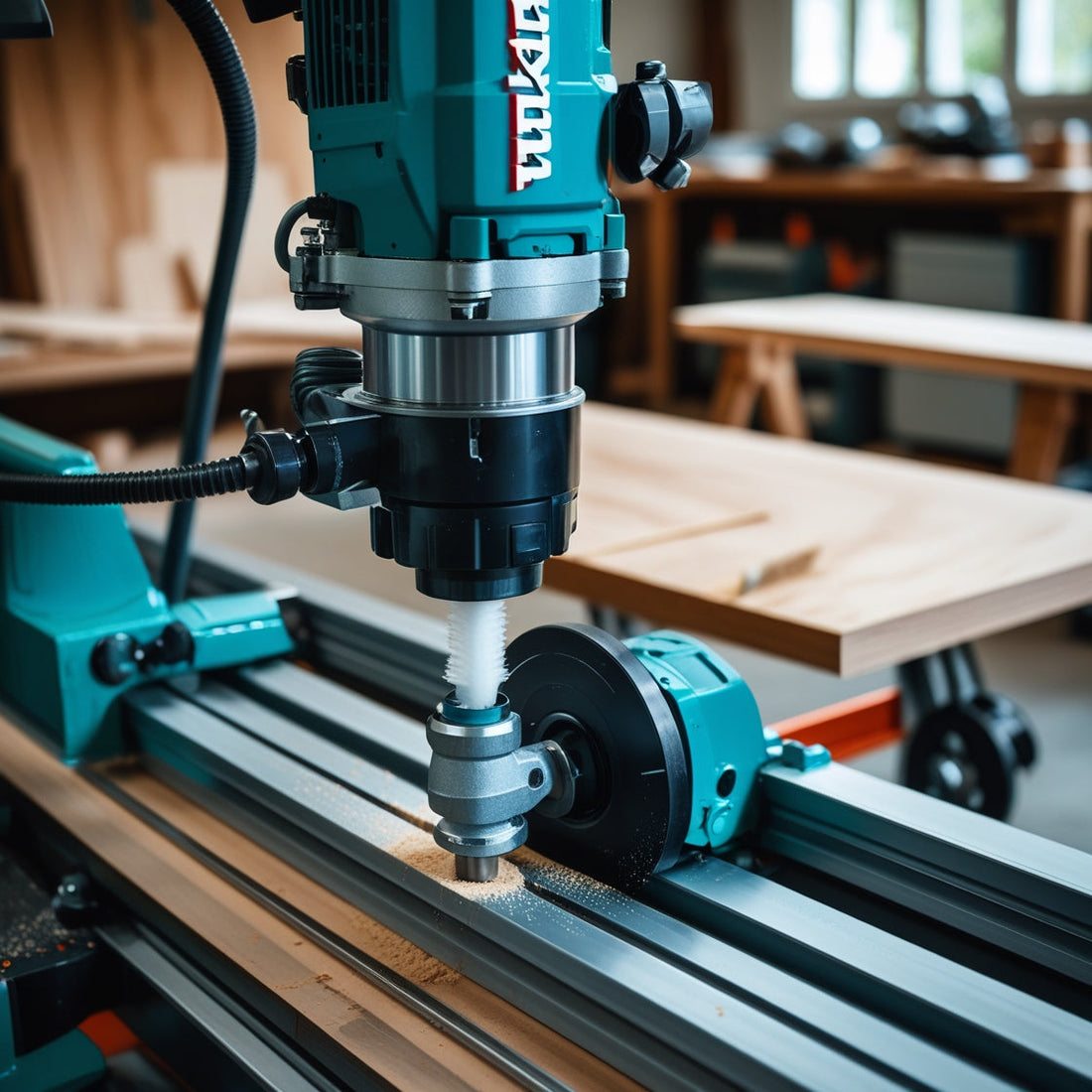


Industrielle Anwendungen: Optimierung von Produktion und Effizienz – Ein umfassender Leitfaden
Industrielle Anwendungen: Ein vollständiger Überblick
Industrielle Anwendungen stellen einen sich ständig weiterentwickelnden Bereich dar, der für die Optimierung von Produktionsprozessen und die Verbesserung der Wettbewerbsfähigkeit von Unternehmen von entscheidender Bedeutung ist. Sie umfassen eine Vielzahl von Technologien und Lösungen zur Verbesserung der Effizienz, Produktivität, Sicherheit und Rentabilität industrieller Abläufe in allen Branchen: Fertigung, Energie, Agrar- und Lebensmittelindustrie, Logistik usw. Von der präzisen Kontrolle der Produktionsparameter bis hin zur vorausschauenden Wartung, kollaborativen Robotik, ausgefeilten Datenanalyse, erweiterter Realität und der intelligenten Lieferkette verändern diese Anwendungen Arbeitsmethoden und Wirtschaftsmodelle grundlegend. Das Hauptziel besteht darin, eine intelligentere, flexiblere und widerstandsfähigere Produktion zu schaffen, die sich an veränderte Markt- und Wettbewerbsanforderungen anpassen kann.
In diesem Artikel werden die verschiedenen industriellen Anwendungen, ihre Vorteile und Herausforderungen im Detail untersucht und erläutert, wie sie zu einer allgemeinen Betriebsoptimierung beitragen. Dabei werden die wirtschaftlichen, ökologischen und sozialen Aspekte hervorgehoben. Darüber hinaus analysieren wir unterschiedliche Implementierungsmodelle und Strategien, um einen erfolgreichen Übergang zur Industrie 4.0 zu gewährleisten.
Die wichtigsten Bereiche der industriellen Anwendungen: eine detaillierte Analyse
1. Industrielle Automatisierung und kollaborative Robotik
Durch Prozessautomatisierung, einschließlich der Integration kollaborativer Roboter (Cobots), können Sie die Produktivität steigern, die Arbeitskosten senken, die Produktqualität und -genauigkeit verbessern und Aufgaben übernehmen, die für Menschen repetitiv, mühsam oder gefährlich sind. Die Automatisierung kann Schweißen, Lackieren, Montage, Handhabung, Palettieren, Qualitätsprüfung usw. umfassen. Industrieroboter werden immer ausgefeilter und verfügen über moderne Sensoren, Bildverarbeitungssysteme und Systeme der künstlichen Intelligenz, die ihnen mehr Autonomie, Anpassungsfähigkeit und die Zusammenarbeit mit menschlichen Bedienern ermöglichen. Die Integration künstlicher Intelligenz ermöglicht außerdem eine bessere Optimierung der Roboterbahnen, Anpassungen in Echtzeit und ein besseres Management unvorhergesehener Ereignisse.
2. Vorausschauende Wartung und Internet der Dinge (IoT)
Durch die Erfassung von Echtzeitdaten von vernetzten Sensoren (Internet der Dinge – IoT), die in Maschinen und Geräten integriert sind, ermöglicht die vorausschauende Wartung die Vorhersage von Geräteausfällen. Durch die Analyse dieser Daten, häufig in Verbindung mit Algorithmen des maschinellen Lernens, können Ausfälle vorhergesagt und Wartungsmaßnahmen proaktiv geplant werden. Auf diese Weise lassen sich teure Ausfallzeiten und Produktionsverluste minimieren. IoT spielt eine entscheidende Rolle bei der Vernetzung und dem Informationsaustausch zwischen verschiedenen Geräten und Systemen und schafft so echte digitale Synergien innerhalb der Fabrik.
3. Prozesskontrolle und industrielle Überwachung
Moderne Steuerungssysteme, die häufig auf SCADA-Systemen (Supervisory Control and Data Acquisition) basieren, überwachen und regeln Produktionsprozesse in Echtzeit und gewährleisten so die Qualität, Konsistenz und Konformität der fertigen Produkte. Diese Systeme ermöglichen es, die Nutzung von Ressourcen (Energie, Rohstoffe, Wasser) zu optimieren, Abfall zu minimieren, die Gesamtleistung zu verbessern und die Produktionskosten zu senken. Durch die Überwachung sind die verschiedenen Parameter zentral überwacht und bei Anomalien oder Abweichungen von den definierten Standards ein schnelles Eingreifen möglich. Digitale Dashboards bieten einen globalen Überblick über den Status des Produktionsprozesses.
4. Energiemanagement und Energieeffizienz
Die Optimierung des Energieverbrauchs stellt für Industrieunternehmen sowohl aus wirtschaftlicher als auch aus ökologischer Sicht eine große Herausforderung dar. Industrielle Anwendungen ermöglichen die detaillierte Überwachung, Analyse und Verwaltung des Energieverbrauchs, identifizieren Verlustquellen und schlagen Lösungen zur Verbesserung der Energieeffizienz vor. Hierzu kann beispielsweise die Nutzung intelligenter Technologien zur Optimierung von Heizung, Klimaanlage, Beleuchtungssystemen, Elektromotoren usw. gehören. Durch die Datenanalyse können Zeiten mit hohem Verbrauch identifiziert und die Produktion entsprechend angepasst sowie der Einsatz erneuerbarer Energien optimiert werden.
5. Qualitäts- und Compliance-Managementsysteme
Qualitätsmanagement ist ein entscheidender Aspekt in der modernen Industrie. Mithilfe spezieller Anwendungen können Sie integrierte Qualitätsmanagementsysteme gemäß ISO-Normen (ISO 9001, ISO 14001 usw.) einrichten und wichtige Leistungsindikatoren (KPIs) in Echtzeit überwachen. Dank digitaler Tools lassen sich die Rückverfolgbarkeit der Produkte, die Qualitätskontrolle in jeder Prozessphase und die Verwaltung von Nichtkonformitäten verbessern. Dies trägt dazu bei, die Kundenzufriedenheit zu verbessern und die durch fehlerhafte Produkte verursachten Kosten zu senken.
6. Arbeitssicherheit und Risikomanagement
Arbeitssicherheit und Unfallverhütung haben höchste Priorität. Industrielle Anwendungen tragen durch Überwachungs-, Warn- und Schutzsysteme zur Schaffung einer sichereren Arbeitsumgebung bei. Hierzu können beispielsweise Gassensoren, Brandmeldeanlagen, vernetzte persönliche Schutzausrüstungen, Risikomanagementsysteme und Unfallszenarien gehören. Durch die Analyse der Daten können Risikobereiche identifiziert und entsprechende Präventionsmaßnahmen ergriffen werden.
7. Künstliche Intelligenz (KI) und maschinelles Lernen (ML)
KI und ML werden zunehmend eingesetzt, um komplexe Daten zu analysieren, Produktionsprozesse zu optimieren, die Bedarfsprognose zu verbessern, komplexe Aufgaben zu automatisieren und Anomalien in Echtzeit zu erkennen. Durch maschinelles Lernen können Systeme aus Daten lernen und ihre Leistung im Laufe der Zeit verbessern und sich an veränderte Produktionsbedingungen anpassen. KI kann für vorausschauende Wartung, Qualitätskontrolle, Optimierung der Produktionsplanung und Entscheidungsfindung eingesetzt werden.
8. Big Data und Predictive Analytics
Durch das Sammeln und Analysieren großer Datenmengen (Big Data) ist es möglich, Trends, Muster und Anomalien in Produktionsprozessen zu erkennen. Mithilfe prädiktiver Analysen können Sie zukünftige Ereignisse wie Geräteausfälle, Nachfrageänderungen oder Sicherheitsrisiken vorhersagen, um fundierte Entscheidungen zu treffen und den Betrieb zu optimieren. Datenanalysen können außerdem dazu beitragen, die Lieferkette zu optimieren, Lagerbestände zu reduzieren und das Ressourcenmanagement zu verbessern.
9. Simulation und digitale Zwillinge
Durch die Simulation können Prozesse virtuell getestet und optimiert werden, bevor sie in der realen Umgebung implementiert werden. Dadurch werden die damit verbundenen Risiken und Kosten reduziert. Digitale Zwillinge, virtuelle Darstellungen von Geräten und Prozessen, ermöglichen die Fernüberwachung, -analyse und -steuerung von Vorgängen und erleichtern die Wartung, Optimierung und Schulung der Bediener. Dadurch können unterschiedliche Szenarien getestet und die besten Lösungen ermittelt werden, bevor sie physisch umgesetzt werden.
10. Augmented Reality (AR) und Virtual Reality (VR)
Augmented Reality und Virtual Reality bieten neue Möglichkeiten für Bedienerschulungen, Wartungen und technische Fernunterstützung. AR ermöglicht die Überlagerung der realen Welt mit digitalen Informationen, wodurch die Wartung und Reparatur von Geräten erleichtert wird. VR ermöglicht die Simulation realer Situationen und die Schulung von Bedienern in einer sicheren und kontrollierten Umgebung.
11. Intelligente Lieferkette
Die Digitalisierung der Lieferkette ermöglicht eine bessere Sichtbarkeit, bessere Koordination und bessere Optimierung des Warenflusses. Industrielle Anwendungen ermöglichen die Echtzeitverfolgung von Produkten, die Optimierung des Transports, die Bestandsverwaltung und eine verbesserte Zusammenarbeit zwischen den verschiedenen Akteuren in der Lieferkette.
Vorteile und Herausforderungen industrieller Anwendungen
Vorteile :
- Deutliche Verbesserung der Produktivität und Effizienz.
- Reduzierung der Produktionskosten und des Abfalls.
- Verbesserung der Produktqualität und -konformität.
- Erhöhte Sicherheit und Schutz der Arbeitnehmer.
- Gewinnen Sie an Wettbewerbsfähigkeit auf dem Markt.
- Optimierung des Ressourcenmanagements (Energie, Rohstoffe).
- Verbesserung der Entscheidungsfindung durch Datenanalyse.
- Erhöhte Flexibilität und Anpassung an Marktveränderungen.
- Verbesserung der Zusammenarbeit zwischen den verschiedenen Akteuren in der Wertschöpfungskette.
Herausforderungen:
- Hohe anfängliche Investitionskosten.
- Erfordert technisches Fachwissen und spezielle Fähigkeiten.
- Komplexe Integration unterschiedlicher Systeme und Technologien.
- Datensicherheit und Cybersicherheit.
- Anpassung an Veränderungen und Schulung des Personals.
- Wartung und Aktualisierung von Systemen.
- Organisatorisches Änderungsmanagement.
Abschluss
Industrielle Anwendungen sind Schlüsselelemente der digitalen Transformation und der Industrie 4.0. Der Einsatz dieser Technologien bietet erhebliche Vorteile hinsichtlich Effizienz, Produktivität, Sicherheit und Wettbewerbsfähigkeit. Eine erfolgreiche Umsetzung erfordert jedoch eine sorgfältige Planung, entsprechendes technisches Fachwissen und ein wirksames Risikomanagement. Die Zusammenarbeit zwischen Herstellern, Integratoren, Beratern und Anwendern ist von entscheidender Bedeutung, um den Return on Investment zu maximieren und einen erfolgreichen Übergang zu einer intelligenteren, nachhaltigeren und widerstandsfähigeren Produktion sicherzustellen. Für die erfolgreiche Implementierung dieser Technologien ist eine klar definierte Strategie, die auch die Schulung der Mitarbeiter und ein organisatorisches Änderungsmanagement umfasst, von entscheidender Bedeutung.
Schlagwortindex :
Industrielle Anwendungen, Automatisierung, Robotik, IoT, vorausschauende Wartung, Prozesssteuerung, Energiemanagement, industrielle Sicherheit, künstliche Intelligenz, maschinelles Lernen, Big Data, prädiktive Analytik, Simulation, digitale Zwillinge, erweiterte Realität, virtuelle Realität, intelligente Lieferkette, Industrie 4.0, Produktionsoptimierung, Energieeffizienz, digitale Transformation, industrielle Wettbewerbsfähigkeit, Qualitätsmanagement, SCADA, KPI, ISO 9001, ISO 14001.